Welding is an art form that combines technical expertise with precision, and mastering miller weld settings is essential for achieving professional results. Whether you're a seasoned welder or just starting out, understanding the intricacies of miller welding equipment can significantly enhance your welding performance. From selecting the right parameters to adjusting amperage levels, this guide will walk you through everything you need to know about miller weld settings.
Welding has become a critical component in various industries, including automotive, construction, and manufacturing. The demand for high-quality welds continues to grow, and having the right knowledge about miller weld settings ensures you meet industry standards. This article aims to provide comprehensive insights into the world of welding, focusing on miller weld settings that can elevate your skills to the next level.
As welding technology advances, it's important to stay updated with the latest techniques and tools. Miller welders are renowned for their reliability and performance, making them a top choice for professionals worldwide. By understanding the nuances of miller weld settings, you can optimize your welding processes, save time, and produce superior results. Let's dive into the details.
Read also:Gregory Abbott Now The Journey Of A Musical Legend
Table of Contents
- Introduction to Miller Welders
- Understanding Miller Weld Settings
- Key Components of Miller Welders
- Common Miller Weld Settings
- Adjusting Amperage and Voltage
- Wire Feed Speed Settings
- Advanced Miller Weld Settings
- Troubleshooting Miller Weld Settings
- Best Practices for Miller Welders
- Conclusion and Call to Action
Introduction to Miller Welders
Miller welders have been a staple in the welding industry for decades. Known for their durability and versatility, these machines cater to a wide range of welding applications. Whether you're working on small-scale projects or large industrial tasks, Miller welders offer the flexibility and power needed to get the job done efficiently.
One of the key features of Miller welders is their ability to handle various welding processes, including MIG, TIG, and Stick welding. This adaptability makes them ideal for professionals who require precision and control over their welding operations. By understanding the basics of Miller welders, you can better appreciate the importance of proper miller weld settings.
Why Choose Miller Welders?
- High-quality construction ensures longevity and reliability.
- Advanced technology provides better control over welding parameters.
- Wide range of models to suit different welding needs.
Understanding Miller Weld Settings
Miller weld settings are the foundation of successful welding operations. These settings determine how the welding machine performs, influencing factors such as heat input, penetration, and bead appearance. Properly configuring your miller weld settings can make a significant difference in the quality of your welds.
Key aspects of miller weld settings include amperage, voltage, wire feed speed, and shielding gas flow rate. Each of these parameters plays a crucial role in achieving optimal welding results. By understanding the interplay between these settings, you can fine-tune your welding machine for specific applications.
Factors Influencing Miller Weld Settings
- Material type and thickness
- Welding process (MIG, TIG, Stick)
- Environmental conditions
Key Components of Miller Welders
To effectively adjust miller weld settings, it's important to familiarize yourself with the key components of Miller welders. These components include the power source, torch, wire feeder, and shielding gas system. Each component contributes to the overall performance of the welding machine.
The power source is responsible for generating the necessary electrical current for welding. Modern Miller welders often feature digital controls, allowing for precise adjustments to amperage and voltage. The torch delivers the welding wire and shielding gas to the workpiece, while the wire feeder ensures consistent wire feed speed. Lastly, the shielding gas system protects the weld pool from atmospheric contamination.
Read also:Comprehensive Guide To Auto Insurance Geico Everything You Need To Know
Importance of Digital Controls
Digital controls on Miller welders offer several advantages:
- Precision in setting adjustments
- Improved user interface
- Memory functions for storing favorite settings
Common Miller Weld Settings
When it comes to miller weld settings, there are several common configurations that apply to most welding applications. These settings serve as a starting point, which can then be fine-tuned based on specific project requirements.
For MIG welding, a typical miller weld setting might include an amperage range of 75-200 amps, depending on the material thickness. Voltage settings generally fall between 18-28 volts, while wire feed speed is adjusted to achieve the desired weld bead profile. Shielding gas flow rate is typically set between 15-30 cubic feet per hour (CFH).
Variations in Weld Settings
- Higher amperage for thicker materials
- Lower voltage for thinner materials
- Increased wire feed speed for faster deposition rates
Adjusting Amperage and Voltage
Amperage and voltage are two of the most critical miller weld settings. Amperage controls the amount of heat generated during welding, while voltage influences the arc length and weld bead profile. Properly adjusting these settings is essential for achieving clean, strong welds.
When adjusting amperage, consider the thickness of the material being welded. Thicker materials require higher amperage to penetrate properly, while thinner materials may warp if too much heat is applied. Voltage settings should be adjusted based on the desired arc length, with lower voltages producing shorter arcs and higher voltages creating longer arcs.
Tips for Adjusting Amperage and Voltage
- Start with manufacturer-recommended settings
- Make incremental adjustments as needed
- Test settings on scrap material before welding the actual project
Wire Feed Speed Settings
Wire feed speed is another important miller weld setting that affects the quality of your welds. This parameter determines how quickly the welding wire is fed into the weld pool, influencing deposition rates and weld bead appearance.
For MIG welding, wire feed speed is typically measured in inches per minute (IPM). Faster wire feed speeds result in higher deposition rates, which can be beneficial for filling large gaps or building up material. However, excessive wire feed speed can lead to poor weld quality, so it's important to find the right balance for your application.
Optimizing Wire Feed Speed
- Match wire feed speed to amperage and voltage settings
- Use trial and error to find the optimal speed for your project
- Consider material type and thickness when setting wire feed speed
Advanced Miller Weld Settings
For experienced welders, advanced miller weld settings offer even greater control over the welding process. These settings include pulse welding, hot start, and arc force, among others. By mastering these advanced settings, you can tackle complex welding challenges with confidence.
Pulse welding is a technique that modulates the welding current in a controlled manner, reducing heat input while maintaining arc stability. This is particularly useful for welding thin materials or when working with heat-sensitive alloys. Hot start and arc force settings enhance arc initiation and stability, improving overall welding performance.
Exploring Advanced Features
- Pulse welding for precise heat control
- Hot start for easier arc initiation
- Arc force for improved arc stability
Troubleshooting Miller Weld Settings
Even with proper knowledge of miller weld settings, issues can arise during welding operations. Common problems include poor weld quality, inconsistent bead appearance, and arc instability. By identifying the root cause of these issues, you can make the necessary adjustments to resolve them.
Poor weld quality may result from incorrect amperage or voltage settings, while inconsistent bead appearance could be due to improper wire feed speed. Arc instability is often caused by incorrect shielding gas flow rate or poor electrode contact. Troubleshooting these issues requires a systematic approach, starting with a thorough inspection of all welding parameters.
Common Troubleshooting Tips
- Check all connections for proper tightness
- Verify shielding gas flow rate
- Test settings on scrap material to identify issues
Best Practices for Miller Welders
To maximize the performance of your Miller welder and achieve consistent results, it's important to follow best practices. These practices include regular maintenance, proper setup, and adherence to safety protocols.
Regular maintenance ensures your welding machine operates at peak efficiency. This includes cleaning the torch and nozzle, inspecting the wire feeder, and checking the shielding gas system. Proper setup involves selecting the correct miller weld settings for your application and ensuring all components are functioning correctly. Lastly, always follow safety protocols to protect yourself and others during welding operations.
Essential Maintenance Tips
- Inspect and clean the torch regularly
- Check wire feeder for proper alignment
- Verify shielding gas system for leaks
Conclusion and Call to Action
In conclusion, mastering miller weld settings is essential for achieving professional-quality welds. By understanding the key components of Miller welders and properly configuring your welding parameters, you can optimize your welding processes and produce superior results. Whether you're working on small-scale projects or large industrial tasks, the right miller weld settings can make all the difference.
We encourage you to share your experiences and insights in the comments section below. Have you encountered any unique challenges while adjusting miller weld settings? What tips and tricks have you discovered along the way? Additionally, feel free to explore other articles on our site for more welding tips and techniques. Together, let's continue to elevate the art of welding!
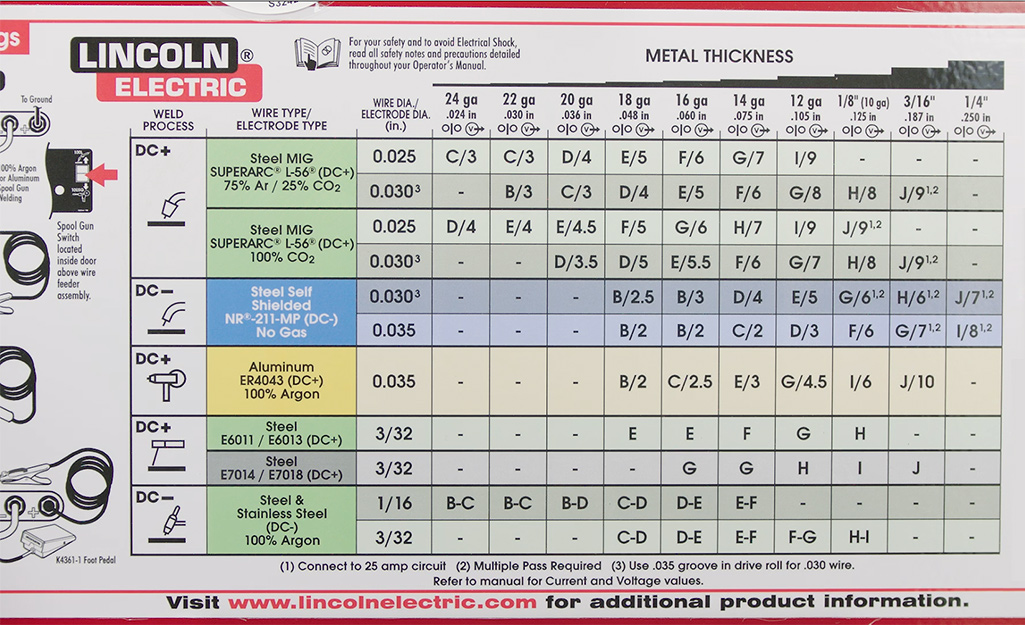